Happy Halloween!
What better way to spend Halloween then performing quality tests on caskets. Working under tight deadlines and the demise of an old design, a group of us gathered together to validate several alternatives in a new casket design. Yes, even caskets have rigid quality criteria to satisfy our customers.
Prior to testing, several different opinions were strongly expressed as to which specific design would be best. When facing a deadlock, the best approach is to go to gemba and test all alternatives. Let the data guide you! The actual test results changed many perceptions which will determine the final outcome. (The approach was expressed in The Game of Rock-Paper-Scissors post).
It worked for us today!
Mike Wroblewski's blog on developing a Kaizen Mind focused on Lean Manufacturing, Lean Healthcare, Lean Government and Six Sigma Quality
Monday, October 31, 2005
Sunday, October 30, 2005
Visual Management in Lean Manufacturing Means Seeing the Problems
Visual management brings many things to mind when applied to lean manufacturing principles. We think of plastering charts, graphs, pictures, color coding, labels and work instructions all over our plant like wall paper. Just as in the case of work instructions, (see posting visual work instructions), this is just a partial truth. In the lean approach, visual management is more than just charts and pictures.
Based on what I was taught about the Toyota Production System, visual management is about seeing. Seeing the waste, seeing the problems, seeing the things needing improvement in addition to seeing the improvements from the eyes of the customer.
In American business, we have an extremely difficult challenge in seeing. We do not like to see problems and we overlook waste as just a cost of doing business. We get defensive when problems are brought to the attention of management (The higher up the organization, the more defensive). In the shuffle to deflect blame, we stumble through the improvement process hoping it will get better. Unwritten policies are followed like "never shut down the production lines" or "we need the parts now so write an UAI (Us As Is) disposition".
To move forward on your lean journey, you must first recognized this weakness in American business. Open your eyes in Gemba. You can not improve what you do not see.
Based on what I was taught about the Toyota Production System, visual management is about seeing. Seeing the waste, seeing the problems, seeing the things needing improvement in addition to seeing the improvements from the eyes of the customer.
In American business, we have an extremely difficult challenge in seeing. We do not like to see problems and we overlook waste as just a cost of doing business. We get defensive when problems are brought to the attention of management (The higher up the organization, the more defensive). In the shuffle to deflect blame, we stumble through the improvement process hoping it will get better. Unwritten policies are followed like "never shut down the production lines" or "we need the parts now so write an UAI (Us As Is) disposition".
To move forward on your lean journey, you must first recognized this weakness in American business. Open your eyes in Gemba. You can not improve what you do not see.
Friday, October 28, 2005
What does my Blog title "Got Boondoggle?" mean?
Several people have told me that they don't quite understand the meaning of "Got Boondoggle?" for my blog title. Well, I picked this title for several reasons.
First, "Boondoggle" is a word meaning waste. Boondoggle is more commonly used to describe a waste found in politics/government, specifically a waste of taxpayer money. More broadly, by asking "Got Boondoggle?", I am just asking if you have waste in your operations/processes. If you answer, "yes", then this blog for you. I just extended the connection to the lean manufacturing principle of waste elimination.
Second, the term boondoggle is unique and stands out from the crowd. This should make it easier to find.
Finally, and more importantly, both of my kids laugh every time I say boondoggle.
First, "Boondoggle" is a word meaning waste. Boondoggle is more commonly used to describe a waste found in politics/government, specifically a waste of taxpayer money. More broadly, by asking "Got Boondoggle?", I am just asking if you have waste in your operations/processes. If you answer, "yes", then this blog for you. I just extended the connection to the lean manufacturing principle of waste elimination.
Second, the term boondoggle is unique and stands out from the crowd. This should make it easier to find.
Finally, and more importantly, both of my kids laugh every time I say boondoggle.
Wednesday, October 26, 2005
Katrina Scare Sparks Anti-Lean Direction
I ran across a couple of frightening articles today. (Must be a Halloween prank, please wake me up from my nightmare!). In the October issue of Logistics Management, they published two pieces that, in my opinion, are promoting anti-lean principles for America's future in our growing complex supply chain. I could not believe what I was reading.
The first piece is an editorial "Are you ready for the next Katrina?" by Executive Editor James Aaron Cooke. In this piece, Mr. Cooke says,"The lean-inventory, just-in-time-delivery supply chain model does not make sense today". All stemming from the supply chain interruption caused by Hurricane Katrina. He goes on to include other Just in Case situations as terrorist attacks and shortages in transportation as reason to go anti-lean. He also states, "stockpiling inventory is only the first step," pertaining to needed actions of disaster-preparedness plans. The scariest part is that I can visualize many American executives nodding their heads in agreement to these scare tactics.
The second article is "Shippers see inventory rising," by Susan K. Lacefield. This article is not as scary and just presents the argument that we should be questioning our lean approach. It is based on current events linking to a survey indicating an increase in inventory by 61% of the respondents. Several statements by people interviewed in this article confirm my opinion that many still do not understand or embrace lean manufacturing principles. What a shame! I loved the quote,"That allows [the suppliers] to improve their manufacturing efficiencies by running larger lots." OUCH!
After reading these articles I predict this is just the beginning. The Anti-Lean approach will become wildly popular in the future, based simply on supply-chain interruption fears. Please wake me up!
The first piece is an editorial "Are you ready for the next Katrina?" by Executive Editor James Aaron Cooke. In this piece, Mr. Cooke says,"The lean-inventory, just-in-time-delivery supply chain model does not make sense today". All stemming from the supply chain interruption caused by Hurricane Katrina. He goes on to include other Just in Case situations as terrorist attacks and shortages in transportation as reason to go anti-lean. He also states, "stockpiling inventory is only the first step," pertaining to needed actions of disaster-preparedness plans. The scariest part is that I can visualize many American executives nodding their heads in agreement to these scare tactics.
The second article is "Shippers see inventory rising," by Susan K. Lacefield. This article is not as scary and just presents the argument that we should be questioning our lean approach. It is based on current events linking to a survey indicating an increase in inventory by 61% of the respondents. Several statements by people interviewed in this article confirm my opinion that many still do not understand or embrace lean manufacturing principles. What a shame! I loved the quote,"That allows [the suppliers] to improve their manufacturing efficiencies by running larger lots." OUCH!
After reading these articles I predict this is just the beginning. The Anti-Lean approach will become wildly popular in the future, based simply on supply-chain interruption fears. Please wake me up!
Point Kaizen #2 Designated Deadline
As explained in Point Kaizen, a process improvement can be accomplished by one person quickly (usually within 1 day). This past week we had a material issue with our metal supplier, rejecting steel coils for nonconformance to standard.
After our Purchasing Manager made a phone call to our supplier, I formally sent them a Supplier Corrective Action Request (SCAR) per our quality procedures. When completing the form I noticed that it contained a deadline for returning it. The designated deadline for the SCAR was "to be returned in 30 days from issue date".
Here we have a material problem needing immediate correction yet our formal document states a 30 day wait to provide corrective action is OK. What mixed messages are we sending out? What "sense of urgency" is conveyed? This designated deadline created a 30 day muda.
Before sending the SCAR out, I changed the completion deadline on the form to "ASAP". Simple, urgent and to the point. For all future SCARs, we expect a quick response. (The form was officially changed in one afternoon).
Some of you may think that "ASAP" is not exact enough of a deadline (for example, making it 3 days would be better). Maybe not, by saying ASAP we expect quick action so it does not sit on a desk waiting for the deadline date for even 1 day. Remember - Sense of Urgency, then follow up!
After our Purchasing Manager made a phone call to our supplier, I formally sent them a Supplier Corrective Action Request (SCAR) per our quality procedures. When completing the form I noticed that it contained a deadline for returning it. The designated deadline for the SCAR was "to be returned in 30 days from issue date".
Here we have a material problem needing immediate correction yet our formal document states a 30 day wait to provide corrective action is OK. What mixed messages are we sending out? What "sense of urgency" is conveyed? This designated deadline created a 30 day muda.
Before sending the SCAR out, I changed the completion deadline on the form to "ASAP". Simple, urgent and to the point. For all future SCARs, we expect a quick response. (The form was officially changed in one afternoon).
Some of you may think that "ASAP" is not exact enough of a deadline (for example, making it 3 days would be better). Maybe not, by saying ASAP we expect quick action so it does not sit on a desk waiting for the deadline date for even 1 day. Remember - Sense of Urgency, then follow up!
Tuesday, October 25, 2005
A Simple Follow-up gets Results
In our eagerness to increase our multitasking we never allow enough time to follow-up. It is more important to successfully complete tasks not to undertake more of them.
Posting Visual Work Instructions
As mentioned in my earlier blog post, we hung our visual work instructions above the work station for each operator resulting in no improvement to our process. The only positive impact was with our customers and some of our management on plant tours thinking they looked great. (another example of looking lean versus being lean).
Save yourself some time and effort, any standard work documentation does not need to be posted above the work station for lean manufacturing. Instead, keep a copy of your documentation accessible at the work station (at ground level). It could be placed in a binder, on a ring, or whatever works in your particular operation. The important thing is to keeping it handy not displayed.
Thanks to Mark Graban at the Lean Manufacturing Blog for stating this point in his comments to my earlier posting.
Save yourself some time and effort, any standard work documentation does not need to be posted above the work station for lean manufacturing. Instead, keep a copy of your documentation accessible at the work station (at ground level). It could be placed in a binder, on a ring, or whatever works in your particular operation. The important thing is to keeping it handy not displayed.
Thanks to Mark Graban at the Lean Manufacturing Blog for stating this point in his comments to my earlier posting.
Stamping out Quality Administrative Muda
The most frustrating element that followed our quality management system was the added administrative activities. In controlling documents, one of these wasteful activities was hand stamping each document by color code ("master", "controlled", "uncontrolled" or "obsolete"). The administrative tasks in this effort is classic muda although some people think of it as a necessary waste.
To eliminate this muda and allow us to focus on more value added activities, we used a kaizen approach. As a result, we moved all the quality documents to a web based intranet. The web file became the master file, complete with administrative rights and controls. On each document we stated (in red letters) that "All hard copies are considered uncontrolled". We also included in our system that you needed to check the web to see the most current revision. When you printed out a document it was already "stamped" as uncontrolled. No more hand stamping required!
To eliminate this muda and allow us to focus on more value added activities, we used a kaizen approach. As a result, we moved all the quality documents to a web based intranet. The web file became the master file, complete with administrative rights and controls. On each document we stated (in red letters) that "All hard copies are considered uncontrolled". We also included in our system that you needed to check the web to see the most current revision. When you printed out a document it was already "stamped" as uncontrolled. No more hand stamping required!
Not so Secret Way to Successfully Implement Lean Manufacturing
Training, Practice, Practice, Practice, Practice, Practice, Practice, Practice, Practice and Practice. Repeat Cycle Forever.
Monday, October 24, 2005
True Purpose of Visual Work Instructions
I noticed something interesting when we posted visual work instructions all over our plant. The operators who helped write the content looked them over, made corrections and never looked at them again. The work instructions were posted above each work station yet nobody looked at them after the first week.
Almost every operator believed that they knew their jobs well enough not to rely on the work instructions. So if the visual work instructions are not for the operators, what is their true purpose?
The first purpose is to document (standardize) the current best way to perform a task or complete a process. Many of our processes in the past were considered tribal knowledge. Only a few people carried that specific knowledge in their heads and passed it on to others as required. Over time, some important information was lost which was either lost forever or forced us to re-learn it. Not a very productive use of resources.
The second purpose is for training or teaching new employees the correct method or process. Depending on word of mouth training from experienced operators leaves opportunities of missing information or compromises in quality. The visual work instruction should contain the proper information and improve the learning curve.
Finally, the visual work instructions provide the basis to audit the process. Using the visual work instruction as the standard work method, any person could check the actual operation against the documented method to ensure adherence to standard. In addition, the standard documented process becomes the baseline for improvement efforts.
Almost every operator believed that they knew their jobs well enough not to rely on the work instructions. So if the visual work instructions are not for the operators, what is their true purpose?
The first purpose is to document (standardize) the current best way to perform a task or complete a process. Many of our processes in the past were considered tribal knowledge. Only a few people carried that specific knowledge in their heads and passed it on to others as required. Over time, some important information was lost which was either lost forever or forced us to re-learn it. Not a very productive use of resources.
The second purpose is for training or teaching new employees the correct method or process. Depending on word of mouth training from experienced operators leaves opportunities of missing information or compromises in quality. The visual work instruction should contain the proper information and improve the learning curve.
Finally, the visual work instructions provide the basis to audit the process. Using the visual work instruction as the standard work method, any person could check the actual operation against the documented method to ensure adherence to standard. In addition, the standard documented process becomes the baseline for improvement efforts.
Sunday, October 23, 2005
Visual Work Instructions Basics
A few years ago, we had a consultant join us to improve our operation. One of the first areas that he focused on was placing large visual work instructions all around the plant. This was not a completely new idea to us. Previously, we had targeted visual work instructions at key areas however he wanted more of them.
Based on his advise, we needed larger (11" x 17") visual work instruction posted high above every work station. He also stressed that the work instructions should be on photo paper and laminated. This meant special paper and new color printers. With these work instruction posted at each work station, he predicted a huge increase in quality first pass yield.
Like most consultants, he had some great ideas but his plan was flawed. In addition, he missed the purpose of the improvement as in the case of the visual work instructions. Regardless, we went ahead with his recommendations for all the obvious reasons. Not surprising, the workstations looked great with all the visuals yet we did not see amazing improvements in our quality when we completed this task. Was this project a boondoggle (waste)?
Not a complete waste just implemented poorly. A few practical work instruction improvements were learned in the process:
Visual Work Instruction Basics:
1. Use regular 8 1/2" x 11" copy paper (Its cheaper, standard and only regular printer needed).
2. Post at each work station at the operator level and make it accessible (Posting high up presents a barrier to updating and requires maintenance help).
3. Have the operators write their own work instruction (Keeps ownership and accuracy high)
4. Use plenty of pictures with brief steps. (If it is too wordy, people will not read them).
5. Update them regularly (Out of date information is worse than no information at all).
Start with these basics to make visual work instructions a better tool in your operation. I will add more about what we learned on visual work instructions in the next few posts. Next topic, what is the true purpose of the visual work instructions?
Based on his advise, we needed larger (11" x 17") visual work instruction posted high above every work station. He also stressed that the work instructions should be on photo paper and laminated. This meant special paper and new color printers. With these work instruction posted at each work station, he predicted a huge increase in quality first pass yield.
Like most consultants, he had some great ideas but his plan was flawed. In addition, he missed the purpose of the improvement as in the case of the visual work instructions. Regardless, we went ahead with his recommendations for all the obvious reasons. Not surprising, the workstations looked great with all the visuals yet we did not see amazing improvements in our quality when we completed this task. Was this project a boondoggle (waste)?
Not a complete waste just implemented poorly. A few practical work instruction improvements were learned in the process:
Visual Work Instruction Basics:
1. Use regular 8 1/2" x 11" copy paper (Its cheaper, standard and only regular printer needed).
2. Post at each work station at the operator level and make it accessible (Posting high up presents a barrier to updating and requires maintenance help).
3. Have the operators write their own work instruction (Keeps ownership and accuracy high)
4. Use plenty of pictures with brief steps. (If it is too wordy, people will not read them).
5. Update them regularly (Out of date information is worse than no information at all).
Start with these basics to make visual work instructions a better tool in your operation. I will add more about what we learned on visual work instructions in the next few posts. Next topic, what is the true purpose of the visual work instructions?
Thursday, October 20, 2005
Make Every Word Count in Quality
The Lord's Prayer has 50 words.
The Ten Commandments have 297 words.
The Constitution of the United States of America has 4,500 words.
Our Company Quality Manual has 10, 572 words.
It took just a little effort to read the entire 55 page quality manual front to back. Then I was told that was there was still more to read. Each of the 20 elements (based on the old 1994 ISO Standard) were additional documents to this core quality manual, totaling about 300 extra pages (which I did not bother to word count!).
WOW! What a large, complex description of our Quality Business System. I asked around the plant to see if anyone else had read the entire set of quality documents. Only 1 out of 100 employees had confessed to actually reading it. I bet this is a common occurrence at more than just one company across America.
I started to realized that this was just another reason why our quality system was not understood within the company. Why was our quality manual was so huge? Could it be simpler? Would the company benefit if we could improve this manual to the point that it would be read by every employee? Would our customers benefit if every employee understood the quality system (processes)? I thought "Yes" and we began to kaizen our quality manual.
It took just a couple of weeks and several revisions later, we had successfully simplified our quality manual to a clear and simple description of our quality system. The final version was now just 1,851 words across 7 pages! We made every word count taking out all the "Extra Noise" we think must be added yet adds no value. Next step, getting every employee to read it. I think its quite possible now.
The Ten Commandments have 297 words.
The Constitution of the United States of America has 4,500 words.
Our Company Quality Manual has 10, 572 words.
It took just a little effort to read the entire 55 page quality manual front to back. Then I was told that was there was still more to read. Each of the 20 elements (based on the old 1994 ISO Standard) were additional documents to this core quality manual, totaling about 300 extra pages (which I did not bother to word count!).
WOW! What a large, complex description of our Quality Business System. I asked around the plant to see if anyone else had read the entire set of quality documents. Only 1 out of 100 employees had confessed to actually reading it. I bet this is a common occurrence at more than just one company across America.
I started to realized that this was just another reason why our quality system was not understood within the company. Why was our quality manual was so huge? Could it be simpler? Would the company benefit if we could improve this manual to the point that it would be read by every employee? Would our customers benefit if every employee understood the quality system (processes)? I thought "Yes" and we began to kaizen our quality manual.
It took just a couple of weeks and several revisions later, we had successfully simplified our quality manual to a clear and simple description of our quality system. The final version was now just 1,851 words across 7 pages! We made every word count taking out all the "Extra Noise" we think must be added yet adds no value. Next step, getting every employee to read it. I think its quite possible now.
Wednesday, October 19, 2005
Boy Scouts know Checklists can make All the Difference
It was the middle of the afternoon on a sunny autumn day in the southern Georgia woodlands outside Albany. We were examining our compass readings, determining our next move on the compass course. Being a young tenderfoot scout in the Boy Scouts at the time, I was eager to prove that I could master the skills of wilderness survival.
We were running around the compass course for over an hour when it hit me. I had the sudden need to do what bears do in the woods. Our camp was nowhere in sight so I looked for the most appropriate spot. Fear quickly raced through my head. I forgot to bring my mountain money! To make matters worse, my fellow patrol members were already out of yelling range.
For those of you not familiar with the outdoor ways, mountain money is valuable paper at moments like these. Despite my failure to "Be Prepared", I looked to mother nature to provide a substitute. Needless to say, it was not the same.
I made it home from that weekend campout with a greater appreciation for planning. My Boy Scout training stressed a simple little tool called a checklist that I did not use at that time. If I had used one, I would have remembered to pack with me that precious paper.
Even to this day, I always make out checklists and double check it!
The same simple tool is used extensively in many other areas with outstanding results. Checklists are used in operating rooms to make sure all things are in order before a surgery and all things are accounted for after the procedure. Pilots use checklists in their pre-takeoff procedures, making sure the plane is in good working order prior to flight.
Checklists are also an excellent tool for lean manufacturing. Set ups, office procedures, quality activities, kaizens and even meetings, can all benefit by using a checklist. It is a simple way to insure that you do not forget important items which can make all the difference.
We were running around the compass course for over an hour when it hit me. I had the sudden need to do what bears do in the woods. Our camp was nowhere in sight so I looked for the most appropriate spot. Fear quickly raced through my head. I forgot to bring my mountain money! To make matters worse, my fellow patrol members were already out of yelling range.
For those of you not familiar with the outdoor ways, mountain money is valuable paper at moments like these. Despite my failure to "Be Prepared", I looked to mother nature to provide a substitute. Needless to say, it was not the same.
I made it home from that weekend campout with a greater appreciation for planning. My Boy Scout training stressed a simple little tool called a checklist that I did not use at that time. If I had used one, I would have remembered to pack with me that precious paper.
Even to this day, I always make out checklists and double check it!
The same simple tool is used extensively in many other areas with outstanding results. Checklists are used in operating rooms to make sure all things are in order before a surgery and all things are accounted for after the procedure. Pilots use checklists in their pre-takeoff procedures, making sure the plane is in good working order prior to flight.
Checklists are also an excellent tool for lean manufacturing. Set ups, office procedures, quality activities, kaizens and even meetings, can all benefit by using a checklist. It is a simple way to insure that you do not forget important items which can make all the difference.
Tuesday, October 18, 2005
Link to What's Holding Back Lean?
Interesting article in the latest issue of Managing Automation - "What's Holding Back Lean?"
Do you see the same barriers to implementing lean in your company?
Do you see the same barriers to implementing lean in your company?
Priority in Lean Manufacturing Goals
"There are four purposes of improvement: easier, better, faster, and cheaper. These four goals appear in the order of priority." Dr. Shigeo Shingo
How often in our pursuit of implementing lean manufacturing principles do we go in the reverse order?
How often in our pursuit of implementing lean manufacturing principles do we go in the reverse order?
Monday, October 17, 2005
To Set a Goal or Not Set a Goal, That is the Question
With the year coming to an end, tis the season to start establishing goals for the next year. Everybody gets together on the task and struggles over what to set for the goals . Regardless if its for plant goals, lean improvement goals, kaizen goals or safety goals, this goal setting process always seems the same to me.
It never fails to come up in our discussion as to why we need a goal? So the group debates the question is it better is to set a goal or not set a goal.
Great quality minds have different viewpoints on this topic. As you may know, W. Edward Deming was not a big fan of goals. His famous 14 points of management specifically calls for the elimination of numerical goals. In his book, Out of the Crisis, he states, "Focus on outcome is not an effective way to improve a process or an activity". On the other side, another great quality mind, Philip B. Crosby supports goal setting. In Mr Crosby's book, Quality is Free, he details the importance of goal setting. He further states that, "All (goals) should be specific and capable of being measured". So which is it?
If you read the details of Dr. Deming's works, his viewpoint is based on the idea that in setting goals we do not have a plan or means to make an improvement to the process. Without this plan, goals are meaningless. This is true.
However, with a plan, the process can be improved towards a goal. According to another expert in the improvement field, Dr, Shigeo Shingo, "Improvement goals serve as the foundation for improvement activities".
Since we had some ideas for improvement, we concluded that goals would be effective. Now the debate really begins, what should we set as the goals?
It never fails to come up in our discussion as to why we need a goal? So the group debates the question is it better is to set a goal or not set a goal.
Great quality minds have different viewpoints on this topic. As you may know, W. Edward Deming was not a big fan of goals. His famous 14 points of management specifically calls for the elimination of numerical goals. In his book, Out of the Crisis, he states, "Focus on outcome is not an effective way to improve a process or an activity". On the other side, another great quality mind, Philip B. Crosby supports goal setting. In Mr Crosby's book, Quality is Free, he details the importance of goal setting. He further states that, "All (goals) should be specific and capable of being measured". So which is it?
If you read the details of Dr. Deming's works, his viewpoint is based on the idea that in setting goals we do not have a plan or means to make an improvement to the process. Without this plan, goals are meaningless. This is true.
However, with a plan, the process can be improved towards a goal. According to another expert in the improvement field, Dr, Shigeo Shingo, "Improvement goals serve as the foundation for improvement activities".
Since we had some ideas for improvement, we concluded that goals would be effective. Now the debate really begins, what should we set as the goals?
Sunday, October 16, 2005
Improve your Problem Solving by Improving your Cause and Effect Diagram
The Cause and Effect Diagram has been around for over 50 years as a tool to help us organize potential root causes in our problem solving. Also called the fishbone diagram or Ishikawa Diagram, this tool is simple and effective when used properly. This is were I commonly find mistakes, this tool is not always used properly.
But creating this diagram is so easy, how could anybody possibly get it wrong? Well, not so much wrong as misguided in use that limits the effectiveness of the tool.
The most popular mistake is with the Manpower branch. Because we see a main branch dedicated to manpower, our problem solving mentality starts searching for "Who" to blame for the problem. Many times, we seek to blame someone for the problem due to lack of training, lack of experience or even worse lack of good sense.
Don't fall in this easy trap. Improve your diagram by digging deeper to link this manpower branch to the other branches-method, machine and material. If you stop at "Who", you are not at a potential root cause!
The second most popular mistake I have seen is limiting the manpower branch to just the employee. Why not include management in the manpower branch? Management plays a bigger role than the employee in practically all processes. It would make more sense to look at the role of management in relation to the problem.
In fact, to improve your diagram just add a management branch. Boy, won't that get some attention! NOTE: Even with a management branch, remember this is not a blame game so don't stop at "Who".
The other common misuse is not to add layered sub-branches. You must go beyond the surface questions to see the potential root causes. Without adding additional sub-branches to make us drill down, we just end up looking at symptoms of the problem.
Try these improvements on your Cause and Effect diagram to see if it helps in your next problem solving session.
But creating this diagram is so easy, how could anybody possibly get it wrong? Well, not so much wrong as misguided in use that limits the effectiveness of the tool.
The most popular mistake is with the Manpower branch. Because we see a main branch dedicated to manpower, our problem solving mentality starts searching for "Who" to blame for the problem. Many times, we seek to blame someone for the problem due to lack of training, lack of experience or even worse lack of good sense.
Don't fall in this easy trap. Improve your diagram by digging deeper to link this manpower branch to the other branches-method, machine and material. If you stop at "Who", you are not at a potential root cause!
The second most popular mistake I have seen is limiting the manpower branch to just the employee. Why not include management in the manpower branch? Management plays a bigger role than the employee in practically all processes. It would make more sense to look at the role of management in relation to the problem.
In fact, to improve your diagram just add a management branch. Boy, won't that get some attention! NOTE: Even with a management branch, remember this is not a blame game so don't stop at "Who".
The other common misuse is not to add layered sub-branches. You must go beyond the surface questions to see the potential root causes. Without adding additional sub-branches to make us drill down, we just end up looking at symptoms of the problem.
Try these improvements on your Cause and Effect diagram to see if it helps in your next problem solving session.
Thursday, October 13, 2005
There is Only One Way to Identify the Root Cause
Quality Quiz:
What is the best way to identify the root cause (major cause) of variation in the process creating a defined problem? You must choose only one answer.
a. The Cause-and-Effect Diagram (also known as Fishbone or Ishikawa Diagram)
b. The Pareto Diagram
c. The 5 Ws and 2Hs
d. The 5 Whys
e. Brainstorming
f. Voting
g. Just blame your supplier and let them figure it out
h. None of the above
The correct answer is (h) none of the above. Why? Because all these methods are widely used to help identify or organize potential root causes or the most likely cause. However, none of them actually can identify the root cause.
The only way and best way is by testing and verifying. Without data to prove that it is a root cause, you only have a list of possible root causes. The root cause will be verified when you can pull it in and out of the process resulting in the problem appearing and disappearing. Think of it as a light switch that can turn the light on and off on command.
What is the best way to identify the root cause (major cause) of variation in the process creating a defined problem? You must choose only one answer.
a. The Cause-and-Effect Diagram (also known as Fishbone or Ishikawa Diagram)
b. The Pareto Diagram
c. The 5 Ws and 2Hs
d. The 5 Whys
e. Brainstorming
f. Voting
g. Just blame your supplier and let them figure it out
h. None of the above
The correct answer is (h) none of the above. Why? Because all these methods are widely used to help identify or organize potential root causes or the most likely cause. However, none of them actually can identify the root cause.
The only way and best way is by testing and verifying. Without data to prove that it is a root cause, you only have a list of possible root causes. The root cause will be verified when you can pull it in and out of the process resulting in the problem appearing and disappearing. Think of it as a light switch that can turn the light on and off on command.
Tuesday, October 11, 2005
The Game of Rock-Paper-Scissors

Did you ever play Rock-Paper-Scissors as a kid?
When I was a kid, this was the ultimate decision maker. Whenever we faced an important decision, like who goes first or who gets to decide what we are going to play next, we played rock-paper-scissors.
Normally, after a count of three, you threw out your hand in the form of either a fist, flat hand or extending two fingers. The paper covered the rock, the scissors cut the paper and the rock smashes the scissors. Each had an equal chance of coming out on top, making the decision.
In the grownup business world, we play a similar game when it comes to making most of our decisions. I call this game opinion-data-perception.
Traditionally, we gather around a table for a meeting and instead of throwing out our hands, we throw our our opinions, data and perceptions. The data covers the opinion, the perceptions cut the data and the opinions smashes the perceptions. Each has an equal chance of coming out on top, making the decision.
So how do you win at this game? Better stated, how can we make better decisions?
Well, if you added people to the meeting, you would get more opinions. You know the saying....everyone has one. But this would complicate the issue and pull us away from making a better decision.
If you provided more data, data would be king. Personally, as an ex-Industrial Engineer, I like this one. Data Rules! However, I have learned the hard way that perception is too powerful of a force for data alone. Especially if the perception is formed at the top of the organizational chart. Besides, adding more data just confuses most people to the point that their eyes start to glaze over and their minds become numb.
So what is the answer?
Perception by gemba. To make better decisions, go beyond the data by going to the gemba!
Go to where the work takes place yourself. See the issues with your own eyes, not just what it says on paper in a report or chart. Touch the problem, hear what the people next to the problem have to say. Use all your senses to develop an improved perception of the problem.
With this knowledge, only then can we make better decisions in our grownup game of rock-paper-scissors.
Monday, October 10, 2005
Serious 5S - The White Glove Test
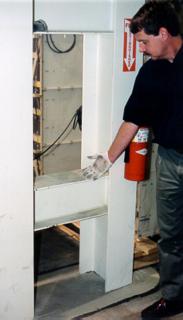
As you begin your lean journey, use 5s as your springboard. The steps to clean and organize the workplace are easy, simple and extremely visible. Benefits are immediate and more importantly, the change process starts off in a positive direction.
Looking only at the cleaning step of 5S, most companies do a good job. However, doing only a good job does not set the standard high enough. Set your 5S program apart from a simple housekeeping exercise, get serious and use the white glove test.
Break out a pair of white gloves and start wiping everywhere. Don't limit yourself to just equipment and tools. Run your white glove across walls, on posts, over beams. Wipe high, wipe low, get on a ladder and wipe higher.
Setting a high standard on a simple process like cleaning will raise the expectations on all the improvement activities that follow.
Thursday, October 06, 2005
Simple Work Aid Solves Packing Problem
At a local manufacturing company, one of their packing lines had a history of customer complaints regarding missing components. Customers were threatening to drop them while return and sorting costs keep growing. This company tried audits, 100% inspection, intensive training, incentives and even disciplinary action yet components still ended up missing from the boxes.
After a series of problem solving sessions along with some experimentation, they added a simple visual work aid that solved the problem. By placing digital pictures of the components with quantities on a large, laminated sheet of paper, they constructed a standard template for each packaged assembly. Using a tray with the template, operators on the assembly line placed components on top of the corresponding picture in the quantities specified. The last operator in line visually checked the tray for completeness than placed the components in the box.
This simple solution only added a slight amount of double handling to the process and eliminated the more expensive audits, inspections, returns and sorting activities.
Watching this work aid in action, several opportunities quickly came to mind where I could implement the same concept. Try it out, modifying it to fit your application, and see if it makes an improvement.
After a series of problem solving sessions along with some experimentation, they added a simple visual work aid that solved the problem. By placing digital pictures of the components with quantities on a large, laminated sheet of paper, they constructed a standard template for each packaged assembly. Using a tray with the template, operators on the assembly line placed components on top of the corresponding picture in the quantities specified. The last operator in line visually checked the tray for completeness than placed the components in the box.
This simple solution only added a slight amount of double handling to the process and eliminated the more expensive audits, inspections, returns and sorting activities.
Watching this work aid in action, several opportunities quickly came to mind where I could implement the same concept. Try it out, modifying it to fit your application, and see if it makes an improvement.
Wednesday, October 05, 2005
New Orleans City with Nonessential Workers
On his Lean Manufacturing Blog, Mark's post on "Nonessential Workers" links to an interesting Boston Globe article. The mayor of New Orleans plans on cutting 3,000 nonessential workers from the city payroll. I agree with Mark, it is insulting to be called nonessential but what do you expect in dealing with the government.
But what about Former President Bill Clinton's suggestion to move relief specialist out of Washington DC and into the storm area to speed things up. I salute you, Mr President, for your Go to the GEMBA approach!
But what about Former President Bill Clinton's suggestion to move relief specialist out of Washington DC and into the storm area to speed things up. I salute you, Mr President, for your Go to the GEMBA approach!
Inspection is never a Root Cause
As I wrap up my monthly quality reports for corporate, I had the opportunity to review a quality report from another division. Everything looked in good order except for one section.
In this section, the quality report listed two units found with defects in their finished goods audit. The resulting corrective action was to show the defects to the inspectors and they were "told to be on the lookout". No other actions were listed.
Statistically, I estimate the probability that these defects will be found again in a future audit or found by the customer is 100%. I agree that training and quality awareness are important. However, this action does not solve the problem. The root cause of any defect is never the inspection process.
To improve your process, look for the root causes that created the defects in the first place. Focus efforts on preventing the problem, not improving your ability to catch the problems through inspection.
In this section, the quality report listed two units found with defects in their finished goods audit. The resulting corrective action was to show the defects to the inspectors and they were "told to be on the lookout". No other actions were listed.
Statistically, I estimate the probability that these defects will be found again in a future audit or found by the customer is 100%. I agree that training and quality awareness are important. However, this action does not solve the problem. The root cause of any defect is never the inspection process.
To improve your process, look for the root causes that created the defects in the first place. Focus efforts on preventing the problem, not improving your ability to catch the problems through inspection.
Monday, October 03, 2005
How much Inventory is too Much?
Inventory is recognized as one of the seven types of wastes mainly due to the fact that it ties up cash. Following lean manufacturing principles , one can easily see the value of a reduction in high dollar items to a minimum inventory level. But what about low dollar or cheap items?
Does it make sense to expend effort on these items to move to a one piece flow?
How much inventory is too much?
Some of you would say its not worth the effort while others would argue that we should eliminate all waste. Where should we draw the line?
One way to help answer these questions is to look at inventory from a different point of view. Instead of dollars, let's look at inventory in time or days of supply. While working for a company a while back, I complied an inventory listing of all active part numbers and sorted by days of supply. The results were eye opening and I recommend you doing the same thing at your company.
Guess what the longest days of supply for an active part number was found at this company?
It was 46 years. Yes, 46 years. I could hardly believe it myself especially with the company being only 20 years old. To make matters worse, it was a metal part. I wondered how long it would be before it starts to rust. Of course, there is a high degree of probability that a design change would make the part obsolete sometime within 46 years. In this case the part was purchased in volume, at a discount, and considered low dollar at this company (less then $3,000 total value) .
From this perspective, now how much inventory is too much?
LEAN POINT
You may think this is an obvious point, but you would be surprised at the number of companies that overlook it. When on the lean journey, it is not enough to just point everybody in the same direction, you must have measurements/goals that point in the same direction. This includes the Purchasing Department.
Does it make sense to expend effort on these items to move to a one piece flow?
How much inventory is too much?
Some of you would say its not worth the effort while others would argue that we should eliminate all waste. Where should we draw the line?
One way to help answer these questions is to look at inventory from a different point of view. Instead of dollars, let's look at inventory in time or days of supply. While working for a company a while back, I complied an inventory listing of all active part numbers and sorted by days of supply. The results were eye opening and I recommend you doing the same thing at your company.
Guess what the longest days of supply for an active part number was found at this company?
It was 46 years. Yes, 46 years. I could hardly believe it myself especially with the company being only 20 years old. To make matters worse, it was a metal part. I wondered how long it would be before it starts to rust. Of course, there is a high degree of probability that a design change would make the part obsolete sometime within 46 years. In this case the part was purchased in volume, at a discount, and considered low dollar at this company (less then $3,000 total value) .
From this perspective, now how much inventory is too much?
LEAN POINT
You may think this is an obvious point, but you would be surprised at the number of companies that overlook it. When on the lean journey, it is not enough to just point everybody in the same direction, you must have measurements/goals that point in the same direction. This includes the Purchasing Department.
Subscribe to:
Posts (Atom)