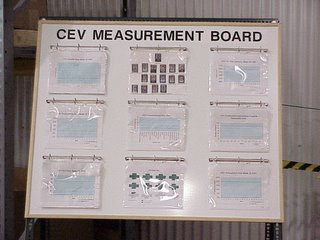
Keep everyone informed by using a department measurement board or dashboard listing the top metrics during your lean improvement journey. For measurement boards to be of any value, here are a few must do rules.
Rule #1 Board Information Must Always Be Current
To be effective, the board must be updated regularly with the latest information. Once the information becomes stale like an old bread loaf on the kitchen counter, it will be useless as an improvement tool.
Rule #2 Boards Display Only Most Important Metrics
When choosing metrics for a company, plant or department, the list grows fast to cover all the possible measures that management deems important to control a business. That's the wrong approach from the old way of "thinking". Remember, you are now "Lean Thinking". That means metrics should be specific to the goals of a lean thinking organization. Measure safety, Measure time (order to customer delivery to payment), Measure quality from the customer point of view (complaints and defect in Parts Per Million), Measure number of improvements, Measure the bottom line.
Rule #3 Promote the Team
The results of each metric is due to the diligence, creativity and basic roll-up-your-sleeves hard work by each team member of the area. Give them the credit for what the metrics display. Put their names and pictures out front for all to see.
Rule #4 Boards Show Future Action
It is important to show the metrics and achievements of the department on the board. Track progress, be proud of the accomplishments and recognize the team. But in reality, it looking at life through the rear view mirror. The measurement boards are also boards of action. List countermeasures, improvement action plans, people responsible and implementation dates. Emphasis should be towards the future on what we are planning to do in addition to the history lesson of what we have already accomplished.
Rule #5 Meet Daily at the Boards
As mentioned many times before, lean manufacturing principles strongly promotes going to gemba. Instead of a typical daily manufacturing staff meeting or production meeting held in the conference room, go around to each of the department board for the updates. Have the leader or even an individual team member update the group from the board. It will certainly promote the importance of the metrics for all to see and give others the chance to see improvements at gemba. Improvements can be seen in 3-D on the shop floor better than any paper report.
3 comments:
Larry,
Thanks for the great comment and added rules. Looks like I can add to my list. I have mentioned ownership labels on an earlier posting. The goodness direction happened to be my next posting. You are a step ahead.
Check on the plane symbol method if it is stll being used. I would guess that after 9-11 that the red plane headed to the ground may offend some people or make them uneasy.
Thanks for reading!
Mike
Richard Kunst of La-Z-Boy in Canada did a nice article on using "report-out" boards to keep managers and others connected to each workstation in a plant. It was in SME's "Lean Directions" e-newsletter - my editorial baby. You can get the article at http://www.sme.org/cgi-bin/get-newsletter.pl?LEAN&20060209&2&
Karen
In the manufacturing plant where I work as a Continuous Improvement Specialist, we love our LDMS Boards.
One challenge that we face though is that we are unable/unwilling to hold our daily meetings at the boards because the noise from the rest of the plant is too loud and distracting. The boards are on wheels and can be rolled in to the conference room, but that is clearly waste.
Any ideas?
Post a Comment