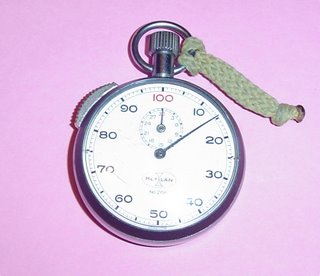
There are many helpful and simple lean tools to use on your lean journey however one tool stands out above all others. The basic stopwatch has proven itself to be the best lean tool available. Like a compass to a hiker, a stopwatch is to the lean practitioner.
The focus of lean manufacturing is to eliminate waste in your process and improve your value stream. The measurement of your success is found in your process timeline which is best measured with a stopwatch. Some might argue that a calendar is a better tool with some processes but I will save that point for another day.
What other tool is the best decision maker of a lean improvement where time is the key determining factor? A stopwatch is unbiased and simply tells you how much time an activity takes without playing favorites. In the past, I have found instances where people would spend hours arguing the merits of one method over another method. In most cases, either no decision could be agreed upon or one party gives up in frustration. A better approach is to put aside the power plays and let the stopwatch determine the best method. Instead of wasting time debating who's ideas is better, go to gemba and try both methods while the stopwatch measures the results. Let the stopwatch lead your way.
Helpful lean hint: Try to get in the habit of measuring time in seconds. If you use minutes or hours, people tend to think in those larger terms and believe 1 hour is quick. If you use seconds, it places emphasis on your lean journey that every second counts.
3 comments:
I'm a recent convert to the idea that a video camera (with a time/date stamp on screen) is an even more helpful tool. I do remember, however, that this isn't allowed in many union environments. That's too bad. A video camera really helps you study the detail of an activity or motion. The extra advantage with video is that the person doing the work can actually watch and analyze themself with you.
The genius of Toyota was to take the stopwatch out of the hands of the elite industrial engineer and put it in the hands of the shop-floor workers in the cell. A little introduction and they could come up with the same improvements, but didn't have a mistrusted guy/gal standing there telling them they weren't working fast enough.
Many more formerly "engineer" tasks were successfully trusted to the workers - see the "shop-floor" series of books published by Productivity Press.
Some of us outside of toyota are doing the same thing. Coach "workers" to see waste themselves and to study each other as a team. It turns them into "thinkers". It's the core of toyota-style "respect for humanity."
Post a Comment