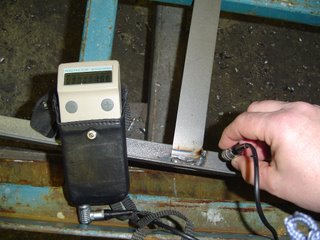
A recent quality issue occurred with one of our suppliers of pre-coated steel. This steel material has a designated specification for paint thickness with a typical +/- allowable tolerance. In our application, the coating needed to be just thick enough to deter rust yet thin enough to allow proper welding.
On a recent shipment, our welders were having a difficult time welding the steel. With our positector, a devise used to measure coating thickness, we quickly measured several samples and found that the coating thickness was all over the map. In some cases, the measured thickness was well over the tolerance range by 3 times the specification causing the welding problem.
We contacted our supplier on this problem. In response, our supplier provided their quality check data from this lot showing everything measuring within tolerance. They suggested that we change the specification if this was not working for us. Our supplier believed that their process was in control even though what we measured on the actual parts did not match their data. To help our supplier in their investigation, we returned several pieces of the nonconforming material.
A few days later, our supplier humbly apologized for the inconvenience caused by these nonconforming parts that were clearly out of spec. When they dug a little deeper in their investigation, they discovered that the quality check procedures were not being followed. The first shift operation was only making 2 checks instead of 10 checks while the second and third shifts were not doing any of the 10 quality checks. All the shifts just filled out the quality check sheet with random numbers to show that 10 checks were completed and within acceptable limits. When management reviewed the reports, everything looked good.
Our supplier assures us that the supervisor has been informed of the problem and that the quality checks are now being performed according to the proper procedures. To their credit, the next shipment was acceptable.
With clearly defined procedures in place, we assume people are doing their quality checks, but are they??? Maybe not! Worse yet, do you find out on your own or when your customer complains?
As a lean thinker, would you accept this suppliers corrective action? How confident would you be that these parts will remain within acceptable tolerance? What course of action would you take if you were this supplier?
Using lean manufacturing principles as our guide, here are several suggestions that may improve our suppliers quality checks.
#1 VERIFY, VERIFY and VERIFY
The first course of action is to verify that the quality checks are being correctly conducted. Regular process audits and a solid verification process will provide the frame work of monitoring your "real" process output.
#2 Genchi Genbutsu
Follow the principle of genchi genbutsu which means "going to the place to see the actual situation for understanding". Management should not rely on reports to understand the process or determine how things are running in their operation. Go out to the shop floor and see for yourself.
#3 Poka-Yoke
Quality checks are fine however preventing the problems in the first place is a better course of action. Put poka-yoke or mistake proofing devices into place. Yes, the more poka-yoke devices the better. Make the process error proof and put countermeasures in place to improve the process.
#4 Keep it Simple
Increasing inspection and adding complex quality procedures will not solve the problem. Why did the employees not follow the original quality plan of 10 quality checks? Ask the 5 whys to get at the root cause. Maybe the quality check process was too complex. Work with the operators to develop a simple, easy quality check plan.
2 comments:
I saw this same thing happening at a major automaker plant in the mid-90's, making major components for an assembly plant. The operators just checked the boxes and fudged data and management didn't give a crap. Ultimately, this is a management issue at your supplier, they either don't care or don't know what they're doing. I'd start looking for another supplier if you can find one.
Mike - so what do you think the final resolution will be? Is someone from your company going to visit their gemba or are you relying on reports from them? As long as you get zero defects, zero questions will be asked? I hope you get it all worked out.
Post a Comment