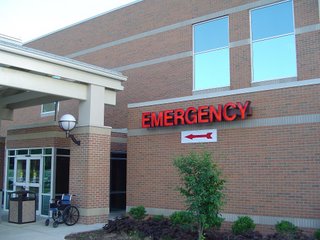
I read an interesting article recently on the Study of Emergency Room (ER) Wait Times in the United States. Apparently, my home state of Indiana ranked 16th out of 49 states in the study so we are a little better than average. According to the article, the national average wait time is 3 hours, 42 minutes. Iowa was the nation's best with an average wait time of 2 hours 18 minutes while those seeking emergency help in Arizona waited a painful 4 hours and 57 minutes on average. This is just the average in each state, not the range from high to low. Makes me wonder what the variation was in the wait time. This measurement is not comforting especially if you are one of the unlucky patients on the upper end of the bell curve! Yet, there is more to this story.
The focus of the article centered on the need for hospitals to start seeing patients as customers and the patient satisfaction level linked to long waits. First of all, I have the highest level of respect for all the doctors, nurses and the entire ER staff for their skill and dedication in saving lives. I always assumed as a patient that we were already thought of as a customer by the ER staff. Well, at least the very few times in my life I experienced the services at an ER, the staff displayed extreme compassion and outstanding responsiveness to the medical emergency surrounding my family. I guess from the medical side of the equation that may be a false assumption across our nation.
I do not consider the ER environment your typical model of a service provider and customer. Can you imagine a patient (customer) shopping around for an ER while needing emergency medical attention? Or a patient (customer) leaves an ER due to the long wait as if we were at a restaurant waiting for a table? The biggest factor in my opinion is that in typical service models, it is a first come, first serve system and the ER service model is based on severity of the medical emergency determining the priority. As a result, some people who use the emergency room may have to wait longer if their "emergency" is not life threatening to allow other patients with urgent medical needs to be treated first. Yes, some patients will cut in line ahead of others to save a life increasing the wait time for some of us. I would not want it any other way!
However, from my lean manufacturing point of view, I see the need for improvement in our healthcare system including the ER setting. The lean healthcare focus is beginning to spread across our nation to address some of the wastes without compromising the health and welfare of patients. Since time is one of the major factors that may help save lives, the velocity of the value stream to treat a patient should be constantly improved. With healthcare cost soaring, the entire healthcare system merits observation, study and analysis to determine improvement opportunities.
One point in the article that really jumped out at me was the "solution" to the long ER wait suggested by one consulting firm. They suggest that by regularly communicating with the patient their status in queue while they waited, the patient level satisfaction level will be higher compared to patients left in the dark waiting for medical treatment. Although the data may support some increased level of satisfaction, this recommendation is just a big band-aid. It accepts that status quo of long waits instead of seeking out the root causes and setting in place the proper counter measures.
But upon reflection, I see that we have this same mindset in manufacturing. How many of us guilty of looking for "trick" ways to improve the measurement and ignore addressing the root cause of the problem? How many of us have added secondary operations like reaming, repairing, trimming, wiping, cleaning, touch-up, grinding, etc, to compensate for a problem to keep our lines running and never address the root cause of the problem? When our manufacturing emergency hits, we put in the band-aid fix at break-neck speed to get our lines back up and running or make the parts pass. We are manufacturing heroes! Hurray!
We all agree that this band-aid fix is just temporary until we get a chance to fix the real problem. How long do we define temporary? Is it one shift? Is it just until the next day. Is it next week? Is it just until our plant shutdown? Maybe never?
Do we as manufacturers manage our resources like in the ER where the severity of the problem determines the priority of our response? Sure we do. However, unlike the ER where every medical case is addressed, many problems in manufacturing are never fixed. Our band-aid becomes the permanent fix and we accept the waste created as just the cost of doing business. How many band-aids exist in your manufacturing process today?
2 comments:
From my experience working with healthcare, one problem is that nurses (for example) are constantly band-aiding and working around the hospital's completely broken processes. Authors like Steve Spear are focusing on how healthcare needs to really put root cause problem solving and root cause solutions in place. I've seen people fight the same fires each and every day, their goal is just to survive the day. You have to create some stability (through standard work), then work on kaizen. One advantage healthcare has is that nurses are in such short supply (in most places), that they don't have to worry about lean leading to layoffs.
Jamie Flinchaugh also wrote about lean healthcare today at my blog:
http://kanban.blogspot.com/2006/06/evolution-of-lean-in-healthcare.html
We do shop around for ER service. I think each of us in a metropolitan area has a "default" ER we visit whenever an emergency comes up.
And you can shop, if not in a life-threatening situatuin. My husband and I drove around one Sunday afternoon when he had an attack of kidney stones. That was futile, but luckily his attack subsided on its own.
Our local ERs have been competing on wait time - one trumped another with a 29-minute wait as opposed to 30 minutes.
My experience was that the waiting room size was much reduced, and I did get my vital signs taken immediately. But I still waited hours in an examining room (not a curtained-off cubicle) with a low-priority back strain.
An aside - when my 14-year-old son cut his foot some years before all this, we jumped to the head of the line. We had to wait a bit when the ER team had to resuscitate a guy who'd been dropped and left, having OD'd on something. We could hear it all because we were only separated by curtains. I hope that acted as a deterrent to any experimenting with hard drugs. (He's 32 now and a productive member of society.)
Post a Comment