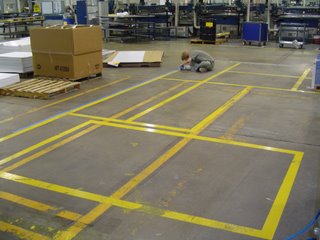
I spent yesterday at a client's manufacturing plant conducting a 5S Day. The 5S stands for Sort, Straighten, Shine, Standardize and Sustain to create an organized, clean and productive workspace. This 5S day was held on a Saturday when normal production was not scheduled to run allowing the team to focus on the target area and not disrupt daily production. We started the day with a quick 1 hour 5S training session followed by working in the target area on the first 3 S of Sort, Straighten and Shine. Our 5S team included members of their management, associates and even temporary help working side-by-side to transform our target area from one of typical chaos to organized flow.
One of the dilemmas facing the team was how to improve the manufacturing floor. As shown in the picture above, this area has falling into a multiple footprint trap. Since this company began their lean journey just last fall, they eagerly jumped into it with both feet. Over the course of about eight months, They have already completing over 20 kaizens throughout the plant. Our target area changed several times from previous kaizen activities causing footprints to change and increase in numbers. The problem is that the majority of the footprints were painted on the floor and old ones were never eliminated.
The purpose of footprints is to designate a home location. As you kaizen an area, if outdated footprints remain on the floor and new ones go in, all you get is confusion. I was told that it too much trouble to remove the old footprints.
Not to let a little paint create further confusion, I took a small group aside to tackle the issue. The shop floor was a typical concrete floor, unpainted but sealed. The painted lines criss-crossed the floor with several coats of paint. Our first attempts to scrap up the paint were painfully slow and not very effective. I quickly realized why they previously gave up. Our second attempt called for stronger action. We pouring a combination heavy duty paint thinner on the lines plus aggressive hand scraping. It worked however it still was not the fastest job of the day. After lots of elbow grease, the old footprints were eliminated.
The team members discussed the line issue trying to decide if paint or tape was the best solution for the future. Paint is more durable but more difficult to change for future kaizens. Tape is very flexible for change but wears out quicker. With some debating, the team arrived at a unified solution to go with floor tape. With the certainty of future kaizens, tape is the most flexible option. To help us sustain the improvements, monitoring and replacing the floor tape as needed was added to the walk through 5S evaluation form as a special item.
8 comments:
There is some 3M plastic tape that works very well on floors and is pretty durable. Forktrucks will tear it up eventually, but you just have to put the tape on a "PM schedule" of sorts. If the tape is a little torn, but it still serves its purpose, I'd asume that is OK. The point is to reduce waste rather than looking "neat" right?
Do you have an "after" picture?
An input from France
Yes, Lean exists also in Europe !
I'm looking for a visual color standard.
Is there anything available ?
I Agree with Mark, Plastic Tape is enough. When too old, it remember us that we need to improve this shop floor
Congratulations for your blog, it helps me to keep the vision and improve my way of animating Kaizen.
Thierry Legrand Aircelle SAFRAN GROUP(Nacelles for Airplane's Motors)
There's a company called Visual Workplace that distributes a product called Floor-Mark. Its goes down like tape, but is fairly durable and is removed with heat. I'm not associated with the company; I just saw it at the IIE conference in May. Our test pieces have been on the floor for a month, and so far, so good. Hope this helps.
We market this material called Brite Mark tape that is 10 times thicker than regular safety tape. Send me your street address and I'll mail you a couple of foot - long pieces.
Luke
Kaizen Products LLC
Seattle, WA
Can also use grey floor paint to paint over the existing markings before you start. If you don't wash your floors but just brush or hoover them, then emulsion lasts long enough and is easier to remove later.
Anonymous from France...
I just ran into this post so the answer may have already been found long ago. But, if anyone is looking for a 5S color standard, we have published a free guide to 5S standard colors. It is available at: http://www.graphicproducts.com/free-gifts/five-s-standard-colors.php
I would recommend Mightyline or Superior Mark. They movable and reusable! http://www.creativesafetysupply.com
I've seen this debate a lot. There is actually a metallic-based decal out there that we've used. Very durable. Basically its a metal sticker that tears much less than vinyl. Cost is comparable but quality and longevity makes it much less expensive than painting or vinyl. They are removable when you work up the edge and peel them up.
The company offers them for marketing but we tested them and used them in our warehouse and production area. Pavementandfloordecals.com.
There's my piece. :)
Steve - Areo
Post a Comment