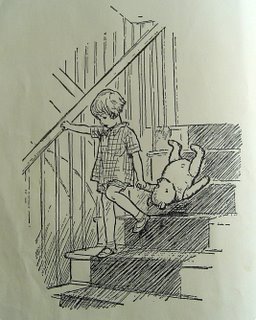
"Here is Edward Bear, coming downstairs now, bump. bump, bump, on the back of his head, behind Christopher Robin. It is, as far as he knows, the only way of coming downstairs, but sometimes he feels that there really is another way, if only he could stop bumping for a moment and think of it."
A. A. Milne, from Winnie-the Pooh, Chapter 1.
Art imitates life, so I am told. Based on what I see repeatedly at manufacturing facilities in America, it seems that a lot of us keep bumping our heads. It amazes me that, very much like Winnie-the-Pooh, we don't take a moment to think. We are too busy with the chaos of running (surviving) the day-to-day challenges of work that we never stop to find another way (a better way!).
For example, how many of us take the time to collect data on our plant efficiencies like First Pass Yield (FPY) and go so far as record the reasons for the non-conformance (putting them in fancy Pareto charts). The next day we repeat the same data collection and chart making activities only to repeat the whole data collect process the following day. (Bump, Bump, Bump!) Yet we never take the time to really go after the root causes of these recurring problems and put in the proper countermeasures (our moment to think).
What about when we collect data like downtime on our assembly lines or equipment complete with stratification by shift, by day of the week, by product? What about our safety audits and injury reports? What about our quality complaints from our customers, returned products and warranty claims? What about our scrap reports? What about our on-time delivery and delivery in-full reports?
Wherever I go, all this information is collected, organized, charted, reported and reviewed yet many times the reports you see on Monday will look strangely similar to the reports from last week, or the week before. Same old problems, different week. (BUMP, BUMP, BUMP).
There really is a better way, if only we can stop bumping for a moment and think of it!
2 comments:
I agree! Surely, there must be a way, there has to be! One time, I heard a friend say that finding the root-cause is all theory. Because according to him, manufacturers sometimes know the root-cause yet out of the same cause a new problem arise. So what do you think should we do in this situation?
Thanks for your comment, Meikah. First off, finding a root cause to a problem is not always easy and sometimes has multiple factors tied to the problem but it is not all theory. Root causes exist. In some cases, as you solve a problem looking at the root cause, another problem may surface. To me that is great news in the sense that we have identified another barrier in our lean path for improvement. Hidden problems are the ones I fear most and the ones that never get solved. Our actions should be to find the best solution to the new problem as well as the old problem. Continuous improvement.
Post a Comment