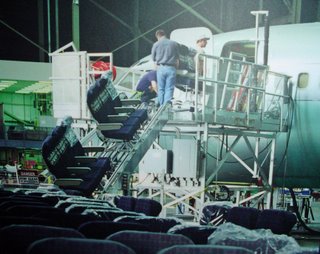
The last couple of months have been tremedously busy for me. That's great from a working point of view however the lack of blogging has been a negative side effect. I will attempt to get back on track and share some of the great things I have seen and learned as I continue on my lean journey.
For the first week of 2007, I am working in Seattle, Washington. Fortunately, I made some free time to visit the Boeing Assembly plant in Everett. I specifically wanted to see for myself some of the lean improvements at Boeing that I have been reading about, like the moving 777 assembly line.
What an amazing manufacturing operation! First off, this plant is by far the largest manufacturing plant I have ever seen. That makes sense for a company with 23,000 employees on site making products like jumbo jets but once you stand in this plant, the huge size simply stuns you. This factory is over 98 acres under one roof, totaling 4.3 million square feet. Just image 911 basketball courts! The ceiling stands 9 stories tall and even the hanger doors are huge-almost the size of a football field!
More amazing for me than the sheer physical size of the plant, is seeing the manufacturing operation of a jumbo jet in person. Even though I just got to see a glimpse of the assembly process, I can appreciate the complexity of the task. The 747 has over 6 million parts and the 777 has 3 million parts. I was told it takes over four months once the parts arrive to build one jumbo jet with a takt time of about one jet every 3 days off the line.
The 777 assembly line was set up as a moving line in September 2006 however for some reason it was not in operation this week. That was a disappointment for me. My tour guide could not provide any details why it was not working. At the end of the line, a huge takt time clock was on display that could be easily seen across the 1/3rd of a mile long assembly line. The best that I could see, everything was on casters from the platforms to the material handling carts. Most of the carts, racks and assorted stations were built with Kaizen pipe. Very little material was stored on the line and all the parts seemed placed in specific floor locations. It also appeared that engineers and other management personal had workstations on the assembly platforms right next to the jets.
Although you could definitely see the progress of a company on a lean journey, like most of us, Boeing still has a long way to go. The work pace appeared downright calm for what I am accustom to seeing in other manufacturing operations. It also appeared that a terrific amount of walking back and forth by employees took place. Boeing has a tough task of pacing work within a 3 day takt time and I did not see any visual indication if that was being monitored or established as standard work.
Unlike what I saw at Toyota, I did not see any problem solving process systems in place for quick reaction at Boeing. Some of you may think that with a 3 day takt time, an andon type rapid response system is not needed. First and foremost, problems need to be seen and not hidden so they can be fixed. The point is to improve the process to fix the problem instead of repeatedly dealing with a problem. It would be way too easy to hide a problem in a 3 day takt time.
Despite what I observed as areas for improvement, the Boeing operation was very cool to see in action. To be fair and accurate to Boeing's lean initiative, if any of you know more about these particular issues and can provide additional insight on how these issues are addressed, I would love to hear about them.
In addition to the 777 line, I looked over the assembly area being set up for the brand new Boeing 787 Dreamliner set for production in 2008. It was easy to see that the lean lessons learned on the 777 and 747 lines will be incorporated into the new 787 assembly line. I can't wait to revisit Boeing in 2008 to see the Dreamliner in operation.
6 comments:
Thanks for taking the time yet again for a trip report!
Honestly, I don't understand the need for a moving line in aircraft manufacturing. I've toured one of the Boeing plants without a moving line, back in 1998.
Is the moving line a case of copying Toyota? How can you have a moving line and NOT have some of the other core lean practices? Does a moving line eliminate more waste than other lean methods could?
I've heard stories, associated with many of the moving line airplane factories, that the the moving line is hardly ever used, that it's just for show or to make certain execs happy, but people don't use it (probably because they don't see any value -- and maybe rightfully so).
So, no real shocker that you didn't see the moving line actually moving.
That's what I would ask about if I had a chance to tour that - why isn't the line moving? That would be a fun "5 Whys" exercise.
Mark,
Great points. The assembly line for the 777 had only 3 planes in line so I would tend to agree with you that the automation of the moving line for this product would be of little value especially with approximately 1 day per station. I don't know the details but I'll bet that some lean consulting advice was taken without question. Now that they have a moving line, I wonder if Boeing's opinion has changed.
Its probably true that they felt the need to experiment with a moving line, but have found it less valuable than other industries. With a 3-day takt time, and only 3 product lines working now, obviously experimentation is a slow process, and its hard to distinguish Lean experiments from proven Lean efforts.
I suggest you look at one of Boeing's other plants in Long Beach, the former Douglas plant which makes C-17. That line pioneered many lean efforts in the early 90s in aerospace before the lean "brand" become so well-advertised. Remember too that since today's Boeing is now a combination of Boeing, Rockwell, Rocketdyne, McDonnell, North American and Douglas, many of its Lean efforts exist outside of Seattle. For another example, check out the F-18E/F line in St Louis.
Why have a moving assembly line? In Boeing's case, the cost/disruption of moving the product (the airplane) may exceed the cost of moving the people and materials to the plane. If Lean only applies to moving assembly lines, there are lots of manufacturing operations that can't (by this narrow definition) employ Lean.
The objective is 1) timeline, and 2) improving the timeline by removing waste. A moving line is a technique, not a goal in and of itself.
Also, I find that Lean practitioners aren't very good at looking at long takt time operations. Maybe becasue it takes more time to "see" what's going on? Not everything is built in high quantity with takt times in minutes or seconds! In fact, the low volume, high mix, longer takt time model applies to most companies who makes speciality machinery and other complex, assemble-to-order products. I was interested to see the "long takt time" post but there is so much more to do in this area.
Mark,
I enjoyed reading your comments on the 777 line. I think you were, on the whole, generous in your assessment of our progress. (Almost full disclosure: I worked on the 777 for 13 years including a stint in the Lean promotion office.)
Moving lines are religious icons for Boeing. During the late nineties, we cut the cycle-time and WIP levels on 777 by 57%; we also set records by continuing to reduce per-unit costs well after our 300th plane (a place where the learning curve often flattens out or even back-slides). But we didn't re-design the factory.
A couple of years later, 737 achieved similar flow and inventory improvements in conjunction with implementing a nose-to-the-door arrangement in Final Assembly (we previously parked the airplanes in "slant positions"). Renton did some amazing work getting the line to move, and today their place is a real show-case: MUCH more impressive than our 777 which still looks like a tornado came through recently.
But here's the kicker: it's by no means clear that 737 reduced recurring costs significantly as a result of their re-design. Mind you, this is closely gaurded information, and I have not seen the data in several years, but the initial returns were not promising.
Nonetheless, we in 777 faced a barrage of questions: when will you guys implement a moving line? Look at the flow 737 took out by making the line move... why don't you guys do the same? (a classic example of: post hoc ergo proctor hoc)
We dragged our feet for a couple of years, focusing instead on ways to reduce set-up time, eliminate defects, and ensure prompt response to delays. The size of our plane, relative to our building made moving the impossible, unless we could achieve two-pieces of WIP in the Final Body Join and Final Assembly areas (a daunting task).
Our main objection, though, was that the point of a moving assembly line (as we understood it) was to make problems visibile, and thus highlight opportunities for improvement. To our eye, we could see plenty of problems -- the problem was getting them solved! There are many structural and systemic dynamics which make it difficult to incorporate improvements rapidly (long, complex supply chain; highly integrated designs; high labor cost associated with re-design and re-planning; low return on investment due to low production volumes; etc.)
Eventually, the 777 leadership was benched in favor of a team made up largely of 737 folks. The re-design you see in the 777 factory is the result of their efforts.
I think the new design is a great idea: body sections move north, join with the wings at the 'top' of the U, and then the line moves south as the sections are joined, tested, etc.
As a share-holder, though, I'm concerned that we spent piles of money to rip up our factory, but did not change the fundamental system for responding to problems and incorporating root-cause counter-measures.
If nothing else, though, the religious zeal the corporate leadership felt for "moving lines" DID enable us to get funding to address some producibility challenges which plagued us since day one. More than anything, it's the improvements in the design of the aircraft that impress me. Ironically, though, these resulted from the PURSUIT of a moving line, rather than the moving line itself.
After leaving 777, I went to 787 where we had the benefit of a clean sheet of paper. When that plane enters production, you'll see a much cleaner, north-to-south line... but it's not going to move.
Given the size of our products and the "multi-linear" or "massively parrallel" build sequence, it is deeply unlikely that you will see the 737 or 777 lines moving continuously any time soon. So long as we apply the TPS principle of stopping the line to highlight problems and ensure responsiveness of support teams, our lines will stop far more often than they move.
Interesting comments. As most lean practitioners know, the moving line is simply a tactic designed to highlight problems and demand immediate or near term fixes. Some of the other issues, moving to next set of tools, etc. are simply side benefits. The power of the moving line is the ability to create urgency by "stopping the line". There are those that suggest achieving that in other ways besides a moving line. That potential has always been there but there is little evidence that anyone has achieved it anywhere in aircraft major assembly.
Lean applies everywhere (lean = common sense & elimination of waste). It always amazes me to hear why it can't work "here" and we are different (gravity is different here). The complexity of the aircraft industry is all the more reason to use moving lines (identify & eliminate problems quickly)not less of a reason. Whatever the challenges are, they are the same for your competitor.
The suggestion that a moving line replaces other lean stratgies/tactics seems odd. The moving line simply makes problems more obvious. Standard work, balance the line, pull, POU, supplier alignment, etc. all need to be applied, but are easier to realize in a moving line.
I have always been amazed at the notion that before we even try the tactics of the "world's best" we know better and will leap frog it with our own brand. How's that been working? Critics of the moving line say it is just a matter of discipline and a moving line is not needed.
I have heard many reasons why a moving line can't work in major aircraft assy. (limited access, too big, low rate, etc.) None of these excuses are real. Learning curves apply regardless of rate. Getting ahead of your competition is the name of the game, not duplicating Toyota's rate.
It does not take a financial expert to know the impact of cutting WIP (i.e. number of 737aircraft in final assy.)in half (22 to 24 versus 11 to 12) on the bottom line. This has been achieved while maintaining a high delivery rate. Inventory holding costs alone are enormous.
Is the moving line the only answer? No, but it sure has great potential. Aircraft have not been stacked up by the lake lately like they were using the slant positions.
Post a Comment